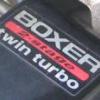
Upgrade Hybrid Turbos
#181
Posted 19 March 2015 - 07:59 PM
#182
Posted 20 March 2015 - 08:00 AM
#183
Posted 26 March 2015 - 01:39 PM
After playing around with a few settings and using the bleed valve on the ICV, vod is now almost non-existent. The map sensor still shows a drop in pressure when the icv opens but there isn't a noticeable drop in power like the more traditional vod. Power feels like it flatlines for a very brief period and then just keeps on picking up when the secondary fully hits.
Power from the secondary is very impressive, the clutch is actually letting go after it hits and although used, the clutch was in good nic when it was put back together so not sure if it is now worn or just not enough clamp.
Primary power isn't really good enough though. The primary is now responding nicely and starting to build boost from just after 2000rpm but wont hit 1 bar until approx. 4000rpm. Makes me wonder whether the headers are the culprit. When on primary, the pulses from 2 cylinders have to take a long path up to the secondary and then back down and across the crossover pipe, could be sapping too much heat and energy from the pulses.
Thought that maybe the larger compressor wheel might combat this by getting some more airflow at a lower turbo speed so I went ahead and ordered some new wheels and housings the other day. Decided to just go with the largest off the shelf wheels available and put them in both turbos. Went with the 20T 11 blade wheels and also ordered 2 x TD04H housings with anti-surge inlets.
I'll pull the motor shortly for when the turbo parts arrive so I will be able to inspect the clutch too and find out if the disc is just wearing out or if it needs an uprated clutch instead.
#184
Posted 03 May 2015 - 02:16 PM
Was stuffed around on my order for the turbo parts as the supplier forgot to send the order so they have only just turned up earlier in the week. I will make an effort to get them installed this week so I can get this thing going again.
The CHRA's need to be machined a little to accept the larger compressor wheels so while I am at it I think I will take to the turbine housings with the die grinder too, just enough to open and smooth the entries slightly.
Here is some shots of the parts:
20T wheel on the left, standard 13T wheel in centre and VF13 wheel on the right. (I had a VF13 that already had it's compressor cover off so thought I would just throw it's wheel in for a comparison shot). The 20T's exducer is slightly larger than the 13T but the inducer is much larger in comparison. Should suck in much more air.
and the compressor housing to suit the new wheels. They have larger intake's and are anti-surge. The anti-surge will probably have no benefit on the primary but will for the secondary at changeover as I was getting mild surge from delaying the opening of the ICV.
#185
Guest_KONG_*
Posted 03 May 2015 - 09:45 PM
Splooged. Awesome man!
#186
Posted 12 May 2015 - 08:34 PM


#187
Posted 13 May 2015 - 09:20 PM
#188
Posted 14 May 2015 - 04:28 PM
Ta, it's just a shame it hasn't got the intended results yet.
Did the secondary last night, I was going to take some step by step photo's of the process to dismantle and reassemble the turbo for a diy but forgot to take photo's of the initial steps. I took a photo of where the chra had to be opened though for the larger wheel. This is after opening it up, the shiny bit is where it was widened.
#189
Posted 14 May 2015 - 04:53 PM
SO how do these compare in size to say a VF35 with P15 rear housing.?
Or the front wheels to the VF32/33
#190
Posted 14 May 2015 - 08:58 PM
I reckon you should throat the exhaust housings out more! there is plenty of metal there... open them up as far as the up pipes and gradually taper them as far in as you can get.
Dont want to choke it up. those wheels should work well if you can keep enough air pushing them
#191
Posted 15 May 2015 - 10:28 AM
I don't have a 32 or 33 at home to take measurements of but I do have a 13,14,18,19 and 25 and they all seem to have very similar specs in regards to compressor inducer/exducer. I did a quick measurement of their inducers earlier and they seem to be around 38mm on the inducer, they all have visibly different designs on the blades however.
Another thread on here had some measurements listed for the 32/33 though and they were listed as:
VF33 ind. 35.6mm exd. 47mm
VF32 ind. 36.5mm exd. 52.5mm
for comparison;
13T wheel 40.65/56mm tip height 4.85mm
20T wheel 47/58mm tip height 4.85mm + tapered tip extension ~ 1.1mm
exhaust wheels:
VF18 45/35mm (approx. I just roughly measured this with a tape)
TD04L 47/40mm tip 7.7mm
TD04 47/40mm tip 6.8mm
I don't have a VF35 to measure either, only had a VF12 from the RS (switched it out for a 23) but the turbine exducer was clearly larger again than the TD04 (closer to 50mm) so google led me to Kando's site where they state the 35 measurements as:
compressor 46.3/60mm exhaust 53/48mm
For turbine housings:
TD04L 6cm -> P12
VF25 P12 -> 6cm
VF18/14 P16 -> 8cm
VF19/32 P18 -> 9cm
VF13 P14 -> 7cm
VF33 P11 -> 5.5cm
VF35 P15 -> 7.5cm (assuming the same R value of ~50mm as is with the TT VF's and TD04)
So the current turbo's are now:
Primary - 20T (47/58) VF25 P12 (6cm) 47/40
Secondary - 20T (47/58) VF14 P16 (8cm) 47/40
to compare:
VF35 (46/60) P15 (7.5cm) 53/48
VF33 (37/47) P11 (5.5cm) 45/35
VF32 (36.5/52.5) P18 (9cm) 45/35
So side by side it would be expected the VF35 would make more power than 1 of the hybrids due to the much larger turbine wheel from less back pressure, but the larger wheel would make the 35 useless on a TT. The other difference's to consider are the 20T wheel is an 11 blade design whereas all the VF wheels are 6+6 design. The 6+6 is better for higher/peaky boost and the 11 blade is better for total flow, theoretically.
The lag form the hybrids vs the standard turbo's is clearly from the larger wheelsets but this of course means they could make alot more power, potentially.
#192
Posted 15 May 2015 - 10:33 AM
I reckon you should throat the exhaust housings out more! there is plenty of metal there... open them up as far as the up pipes and gradually taper them as far in as you can get.
Dont want to choke it up. those wheels should work well if you can keep enough air pushing them
I guess I could. I didn't really take much out, it was just enough from the lips to get them a closer match to the up pipes. The up pipes aren't very big either, 36mmID I think it was. How deep into the turbine should the porting go before it is no longer beneficial? Right up to the entry to the scroll?
#193
Posted 15 May 2015 - 08:05 PM
You want a smooth transition from uppipe to turbo and then go as far as your die grinder will reach! plus port the waste gate holes out but not too far you need a good seat as the flap has some movement this will also help with controlling boost/surge
#194
Posted 17 May 2015 - 05:00 PM
Waste gates aren't used so didn't bother touching them, would actually like to weld them shut but don't really want to risk damaging the housings.



#195
Posted 18 May 2015 - 07:54 PM
Nice work! i gained roughly 40 horsepower atw by using a p16 turbine housing on my primary and countless hours match porting everything and throating out housings when i was still twin turbod! after a retune
Its been a while since i had one but did a vf32 (secondary) have a 10 bladewheel?
#196
Posted 29 June 2015 - 10:44 PM
Been a bit slack again to update this, a few positive changes have been made though. After putting it all back in with the new turbo combo's and taking it for a run I was exceptionally disappointed to say the least. It actually ran worse than before, producing less boost on primary and a shocking changeover. Tried to improve it all by messing with fuel and timing but that was going nowhere either. The poor performance left me with the shits good and proper and I walked away for a few days to clear my head.
When I came back to it I thought I would start over and check the simple things first so started with the tune by pulling timing and adding fuel to get it back to a more conservative level. Then checked the turbo's to make sure they hadn't failed from poor assembly, etc. They had no shaft play or visible damage and with the engine running and charge/intake pipes removed you could see and feel that they were definitely working fine. I hadn't actually tested the pipe work yet to see if there was any leaks under pressure and I also wanted to re-check the pressure holding ability of the butterfly valves so I plugged up the intake piping, set the regulator on the air compressor to 15psi and jerry-rigged it to the pipework. There was a couple of very minor leaks from pinholes in a few of the weld seams, certainly not anything bad enough to effect performance and the short vac line sections on top of the manifold were leaking under pressure. I used 4mm vac line because that was all I had so these have been temp fixed with zip ties until I get some smaller line. The big failure though was the butterfly valve being used as the IACV. This leaked a lot worse than was initially anticipated, it leaked through the shaft out to atmosphere and also leaked across the flap pretty badly. It is also the same valve that was being used as the ECV so it was now obvious that the poor performance was again attributed to valves not doing their job properly. At first I pulled one apart to try and work out exactly where the leaks were coming from and whether I could improve them with some DIY, the shaft leak was easy enough to fix by shimming it up with some teflon tape and washer's, the leak across the flap was too hard without re-machining the seat and using a thicker flap. Gave up on that pretty quick and the next day I got on the phone to Turbosmart and had a chat with them about whether there wastegates and BOV could be re-purposed and do the job, they thought they could work well enough so I ordered the 60mm gate and 50mm BPV through a local distributor (Car Mods Australia - good blokes, I highly recommend them).
The only way to get the gate to fit was to hang it straight off the back of the turbo, not the ideal spot as I think it would of been better deeper into the secondaries dump like the previous 2 valves were fitted but that was the only place it could easily go.
It's a snug fit.
For the initial testing I didn't bother making up the new secondary dump to suit and didn't bother to install the IACV either. The intake pipe was capped and the dump (where the secondary joins at the Y) was also capped. During the first test the gate had a 7psi spring fitted, the bottom port was left disconnected and the top port was connected to a solenoid that switched from atmo to vac so the gate was being held closed by spring pressure only. This didn't work so well as once load increased the exhaust pressure pushed the valve open slightly and caused it to oscillate with a very loud, violent banging as the valve opened and closed against it seat. So took it out and put the 10psi spring in and was still the same result. So applied vac to the bottom port to see if it would hold it shut, this was an improvement as the oscillation wasn't as violent and the primary was building boost but still wasn't right. So as a test, even though it would have been no good as the spring rate would have been too high for the valve to open by vacuum, both 7 and 10psi springs were installed with vac applied to the lower port. This had no improvement to the 10psi spring only. Next was to apply boost to the top port and vac to the bottom port and this worked perfectly, the valve stayed completely shut with zero oscillation. With the valve sealed the primary was able to boost efficiently and easily overboosted - finally it felt like this was getting somewhere. 17psi of spring rate was too heavy to open the valve with vac so the 7psi spring was removed leaving the 10 only. With the ports connected as before the valve would still stay shut and would open when the solenoid's were switched and vac was applied to the top port however the opening rate was very delayed. I checked the vac rating of the vac chamber and it was about 50kpa which is a bit less than what should be needed to overcome a 10psi spring. Switched it out for the 7psi spring, retested and it still managed to stay sealed and once switched would open nicely. Happy days.
Now the gate was sealing properly and the primary was boosting as it should I assembled the rest of the secondaries dump and installed the 50mm 'Big Bubba' BPV into the charge pipe to use as the IACV.
This is with it's temp. plumbing:
It's plumbed so that it can function as a 1 way valve, the throttle side is connected to the exit of the BPV and the charge from the secondary to the intake of the BPV so that as secondary pressure increases it can push the piston up. This works very well as the IACV as no primary boost leaks past the closed piston, the secondary can open it independently and when vac is applied to the port the piston will open fully.
Both valves seem to be suitable for controlling changeover as they are very predictable in their opening in regards to opening at whichever rpm they are commanded to. Initial testing showed changeover was best at closer to 5000rpm (turbos now have a bit more lag with the 20T wheels) but with the ECV set to go from zero flow to full flow the secondary was taking too long to ramp up and the primary was losing boost rapidly in the meantime = VOD. The top port of the ecv was connected to a solenoid that switched from boost to vac at changeover and the bottom port was vac to baro at changeover. As a test the bottom port was disconnected and instead plumbed into the wastegate line (from the actual wastegate) and boost control was set so that it maintained 100% DC under 4000rpm and regulate boost over. This gave the secondary enough prespool to give a much smoother changeover but the downside was at low loads the ecv oscillates slightly. It's not loud and violent like in earlier tests but is enough to be annoying so I am going to replumb a solenoid so that it can go from vac to wastegate duty to initiate prespool. The duty will be tee'd to the wastegate which uses a heavier 14psi spring.
Seems like this project is finally making some ground again.
#197
Posted 29 June 2015 - 10:52 PM
It just amazes me the work in this! Amazing...simply amazing!
#198
Posted 30 June 2015 - 11:24 AM
Ta Matt.
Forgot to mention, the clutch is fine. The bell housing had a bit of oil in it but it wasn't either gearbox oil or engine oil. The rear main was fine (I had only just replaced this too) and the service plate didn't seem to be leaking although it did have a small crack across one of the bolt mounts (this was still the plastic plate) so as a precaution I switched it out for an alloy plate which I was able to raid off a dead ej22 that I have sitting in the garage. The clutch disc itself had this weird grimey, sandy textured paste in the grooves and rivet holes which I am guessing was causing the clutch to slip. My guess is that it was my fault for being too heavy handed with the grease on the clutch fork/pin/etc. when assembling and it all meted and worked it's way onto the clutch. Cleaned it all up, scrubbed the clutch disc and plate and reassembled without any grease this time and so far it hasn't slipped again.
Lesson learnt - clutch + grease = bad.
I also had a crack at welding the internal gates shut but I think I may have forked it up, at least on the primary. I didn't actually weld the flapper as I didn't want to go near the cast housing, so I zip tied the gate shut and simply welded the shaft to the bush both in the housing and at the arm outside the housing.
As in here:
Was good in theory but once the tie was cut off the flapper could still be moved side to side but was still closed tight so left it at that. Once the engine was back in and running though there was instantly this slight chattering noise that wasn't there previously. It sounded very much like the wastegate flap was chattering and it has been getting progressively louder since. The primary is also quite a bit more laggy than previously but that was also to be expected with the larger comp wheel. I am going to pull the housing back off and fix it though because at the very least the noise shit's me.
The 20T wheels are a lot quieter than the 13T wheels also, they still have a loud spool noise but without the high pitched whistle that the 13T's had, sounds a bit more refined. In terms of flow I think the potential is high, as an experiment I disengaged the valves and essentially ran it as a single turbo, it happily held 1 bar through to 6000rpm (as high as I took it on primary only) and maintains a steady air temp till ~4900rpm before it begins to climb by tenths of a degree and at 5300rpm temp begins to climb at a slightly higher rate. I interpreted that as the turbo, at that pressure, is just past it's peak efficiency at ~5000rpm which is kind of perfect since that's about where changeover should take place. Had a few short spurts with more boost too and it doesn't seem to increase air temp either so at early impressions I think these turbos should be capable of quite a bit more boost.
#199
Posted 30 June 2015 - 08:18 PM
Nice use of the external gate... Genius idea! ;-)
#200
Posted 07 July 2015 - 05:39 PM
Nice use of the external gate... Genius idea! ;-)
Yeah I thought so, I probably don't pay enough credit but there has been quite a few inspirational ideas because of other members on this forum. It really is a great group of people here.
Moved some plumbing around in the BBOD again so that the lower port of the ECV would have vac applied under 3900rpm to keep it closed without chatter and over this it would have duty cycle from the wastegate solenoid applied to control boost and thereby also performing pre-spool of the secondary. Also moved some plumbing around for the top port of the ECV. The top port was just controlled by one solenoid that switched from pressure to vac at changeover but with wanting to control pre-spool it now also needed baro applied during the pre-spool stage. The solenoid that was already in use was actually the SPRV solenoid that switched from baro/pressure to vac, just with the baro/pressure select solenoid bypassed for pressure only. So to add the baro into the equation I just had to simply delete the bypass and return the plumbing back to include the baro/pressure select solenoid and add the wire at the ecu. This worked wonders! Wastegate has zero chatter, pre-spool works well as the logs show the secondary beginning to build pressure as the wastgate duty begins to decrease and changeover is so much smoother. Still a lot of tweaking to do to eliminate VOD entirely but I think this should be mostly tune based now.
Re-reading that, it all sounds super confusing but other TT boffins who are familiar with the BBOD should know what I mean. This is a photo of the plumbing in the BBOD:
I ran out of solenoids that had a pressure/vac select so for the lower ECV solenoid that was vac/baro I simply popped off the filter, added a line and tee'd it to the duty solenoid. This is the solenoid second from the right.
0 user(s) are reading this topic
0 members, 0 guests, 0 anonymous users